Live Project Based Catia 6 months training in Noida

KVCH India program builds a powerful training tool that can be implemented in classrooms as well as in the industry. We offer wide range of programs for Live Project 6 Months Catia Training in Noida under the guidance of the best industrial experts. We are continuously awarded for the past 10 years as the Best 6 months Catia training Institute in Noida.
Six Months Catia Training in Noida includes from basic to advance level modules designed for both students and working professionals.
Globalization has brought up with new opportunities in the market creating a pool of jobs for the graduate students. In order to hold up with the everyday growing demand the universities holds the responsibilities to produce students with excellent skills and experience.
6 Months Based Catia Training Course in Noida is very essential to make student who is pursuing MCA, B.Tech, BCA, BBA, MBA course and they should be aware of the real working environment in industries and to prepare them to handle any kind of obstacles that occur. It is a roadway that allows students to apply their theoretical knowledge practically and opens door to new opportunities. At KVCH, we assure that the performance of each student is up to the standards of the IT industry.
At KVCH once the student opts for 6 months Catia Training they get to experience the real working environment of the IT industry. Our team of expert senior trainers work together to ensure the development of set of skills for each individual. Our experts with hands-on experience on the technology and working experience makes sure to deliver the best to the students while working on LIVE project.
KVCH is the renowned 6 months Catia Training Center in Noida providing world class education to students.
Benefits
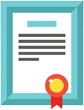
Accredited Curriculum
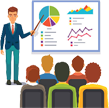
Learn from the Experts
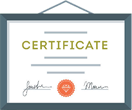
Professional Certificate
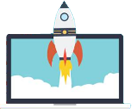
Guranteed Career Growth
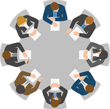
Placement Assistance
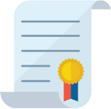
Earn a Valuable Certificate
Course Description
Industrial Training in Catia is a modular 6 months course. The course curriculum of Industrial Training in Catia comprises of
- Introduction to CATIA
- CATIA Workbenches
- System Requirements
- Getting Started with CATIA
- Important Terms and Definitions
- Understanding the Functions of the Mouse Buttons
- Toolbars
- Hot Keys
- Color Scheme
- The Sketcher Workbench
- Starting a New File
- Invoking the Sketcher Workbench
- Invoking the Sketcher Workbench Using the Sketch Tool
- Invoking the Sketcher Workbench Using the Positioned Sketch Tool
- Setting the Sketcher Workbench
- Modifying Units
- Modifying the Grid Settings
- Understanding Sketcher Terms
- Specification Tree
- Grid
- Snap to Point
- Construction/Standard Element
- Select Toolbar
- Inferencing Lines
- Drawing Sketches Using Sketcher Tools
- Drawing Lines
- Drawing Center Lines
- Drawing Rectangles, Oriented Rectangles, and Parallelograms
- Drawing Rectangles
- Creating Points
- Drawing Circles
- Drawing Arcs
- Drawing Profiles
- Drawing Display Tools
- Fit All In
- Pan
- Zoom In
- Zoom Out
- Zoom Area
- Normal View
- Splitting the Drawing Area into Multiple Viewports
- Hiding and Showing Geometric Elements
- Swapping Visible Space
- Other Sketching Tools in the Sketcher Workbench
- Drawing Ellipses
- Drawing Splines
- Connecting Two Elements by a Spline or an Arc
- Drawing Elongated Holes
- Drawing Cylindrical Elongated Holes
- Drawing Keyhole Profiles
- Drawing Hexagons
- Drawing Centered Rectangles
- Drawing Centered Parallelograms
- Drawing Conics
- Editing and Modifying Sketches
- Trimming Unwanted Sketched Elements
- Extending Sketched Elements
- Trimming by Using the Quick Trim Tool
- Filleting Sketched Elements
- Chamfering Sketched Elements
- Mirroring Sketched Elements
- Mirroring Elements without Duplication
- Translating Sketched Elements
- Rotating Sketched Elements
- Scaling Sketched Elements
- Offsetting Sketched Elements
- Modifying Sketched Elements
- Deleting Sketched Elements
- Constraining Sketches
- Concept of Constrained Sketches
- Iso-Constraint
- Under-Constraint
- Over-Constrained
- Inconsistent
- Applying Geometrical Constraints
- Applying Geometrical Constraints Automatically
- Applying Additional Constraints to the Sketch
- Applying Dimensional Constraints
- Applying Contact Constraints
- Applying Fix Together Constraints
- Applying Auto Constraints
- Editing Multiple Dimensions
- Analyzing and Deleting Over-Defined Constraints
- Analyzing Sketch using the Sketch Analysis Tool
- Exiting the Sketcher Workbench
- Creating Base Features by Extrusion
- Creating a Thin Extruded Feature
- Extruding the Sketch Using the Profile Definition Dialog Box
- Extruding the Sketch along a Directional Reference
- Creating Base Features by Revolving Sketches
- Creating Thin Shaft Features
- Dynamically Rotating the View of the Model
- Rotating the View Using the Rotate Tool
- Rotating the View Using the Compass
- Modifying the View Orientation
- Display Modes of the Model
- Shading (SHD)
- Shading with Edges
- Shading with Edges without Smooth Edges
- Shading with Edges and Hidden Edges
- Shading with Material
- Wireframe (NHR)
- Customize View Parameters
- Creating Sections Dynamically
- Maneuvering the Section Plane
- Position of Section Planes
- Assigning a Material to the Model
- Importance of Sketching Planes
- Reference Elements
- Reference Planes
- Creating New Planes
- Creating Points
- Creating Reference Lines
- Other Sketch-Based Features
- Creating Drafted Filleted Pad Features
- Creating Multi-Pad Features
- Feature Termination Options
- Creating Pocket Features
- Creating Drafted Filleted Pocket Features
- Creating Multi-Pocket Features
- Creating Groove Features
- Extruding and Revolving Planar and Non-planar Faces
- Projecting 3D Elements
- Advanced Modeling Tools
- Creating Hole Features
- Creating Fillets
- Creating Chamfers
- Adding a Draft to the Faces of the Model
- Editing Features of a Model
- Editing Using the Definition Option
- Editing by Double-Clicking
- Editing the Sketch of a Sketch-Based Feature
- Redefining the Sketch Plane of Sketches
- Deleting Unwanted Features
- Managing Features and Sketches by using the Cut, Copy, And Paste Functionalities
- Understanding the Concept of Update Diagnosis
- Cut, Copy, and Paste Features and Sketches
- Copying Features Using Drag and Drop
- Copying and Pasting Part Bodies
- Deactivating Features
- Activating Deactivated Features
- Defining Features in Work Object
- Reordering Features
- Understanding the Parent-Child Relationships
- Measuring Elements
- Measuring between Elements
- Measuring Items
- Measuring Inertia
- Transformation Features
- Translating Bodies
- Rotating Bodies
- Creating Symmetry Features
- Transforming the Axis System
- Mirroring Features and Bodies
- Creating Rectangular Patterns
- Creating Circular Patterns
- Creating User Patterns
- Uniform Scaling of Model
- Non-uniform Scaling of Model
- Working with Additional Bodies
- Inserting a New Body
- Inserting Features in the New Body
- Applying Boolean Operations to Bodies
- Adding Stiffeners to a Model
- Generating Solid Combine
- Advanced Modeling Tools
- Creating Rib Features
- Creating Slot Features
- Creating Multi-Sections Solid Features
- Need of Surface Modeling
- Wireframe and Surface Design Workbench
- Starting the Wireframe and Surface Design Workbench
- Creating Wireframe Elements
- Creating Circles
- Creating Splines
- Creating a Helix
- Creating Surfaces
- Creating Extruded Surfaces
- Creating Revolved Surfaces
- Creating Spherical Surfaces
- Creating Cylindrical Surfaces
- Creating Offset Surfaces
- Creating Sweep Surfaces
- Creating Fill Surfaces
- Creating Multi-Sections Surfaces
- Creating Blended Surfaces
- Operations on Shape Geometry
- Joining Surfaces
- Splitting Surfaces
- Trimming Surfaces
- Surface Operations
- Creating Projection Curves
- Creating Intersection Elements
- Healing Geometries
- Disassembling Elements
- Untrimming a Surface or a Curve
- Creating Boundary Curves
- Extracting Geometry
- Transformation Features
- Extrapolating Surfaces and Curves
- Splitting a Solid Body with a Surface
- Solidifying Surface Models
- Adding Thickness to a Surface
- Creating a Solid Body from a Closed Surface Body
- Sewing a Surface to a Solid Body
- Assembly Modeling
- Types of Assembly Design Approaches
- Creating Bottom-up Assemblies
- Inserting Components in a Product File
- Moving Individual Components
- Applying Constraints
- Creating Top-down Assemblies
- Creating Base Part in the Top-Down Assembly
- Creating Subsequent Components in the Top-Down Assembly
- Creating Subassemblies in the Top-Down Assembly
- Editing Assemblies
- Deleting Components
- Replacing Components
- Editing Components inside an Assembly
- Editing Subassemblies inside an Assembly
- Editing Assembly Constraints
- Simplifying the Assembly
- Interference Detection
- Sectioning an Assembly
- Exploding an Assembly
- The Drafting Workbench
- Starting a New File in the Drafting Workbench
- Type of Views
- Generating Drawing Views
- Generating Views Automatically
- Generating Individual Drawing Views
- Generating the Exploded View
- Working with Interactive Drafting in CATIA
- Editing and Modifying Drawing Views
- Changing the Scale of Drawing Views
- Modifying the Project Plane of the Parent View
- Deleting Drawing Views
- Rotating Drawing Views
- Hiding Drawing Views
- Modifying the Hatch Pattern of Section Views
- Inserting sheets in the current file
- Inserting the frame and the title block
- Automatic insertion of the frame and the title block
- Creating the frame and the title block manually
- Adding annotations to the drawing views
- Generating dimensions
- Adding reference dimensions
- Adding datum features
- Adding geometric tolerance to the drawing views
- Adding surface finish symbols
- Adding welding symbols
- Applying weld
- Editing annotations
- Generating the bill of material (BOM)
- Generating balloons
- The Sheet metal Component
- Starting a New File in Generative Sheet Metal Workbench
- Setting Sheet Metal Parameters
- Parameters Tab
- Bend Extremities Tab
- Bend Allowance Tab
- Introduction to Sheet Metal Walls
- Creating the Base Wall
- Creating the Wall on Edge
- Creating Extrusions
- Creating Swept Walls
- Creating Flanges on the Sheet Metal Component
- Creating Hems on the Sheet Metal Component
- Creating a Tear Drop on the Sheet Metal Component
- Creating a User Flange on the Sheet Metal Component
- Creating a Bend
- Creating a Conical Bend
- Bend From Flat
- Creating Rolled Walls
- Creating a Hopper Wall
- Creating a Rolled Wall
- Folding and Unfolding Sheet Metal Parts
- Unfolding Sheet Metal Parts
- Folding Unfolded Parts
- Mapping the Geometry
- Creating Flat Patterns of Sheet Metal Components
- Viewing a Sheet Metal Component in Multiple Windows
- Using Views Management
- Stamping
- Creating a Surface Stamp
- Creating a Bead Stamp
- Creating a Curve Stamp
- Creating a Flanged Cut out Stamp
- Creating a Louver Stamp
- Creating a Bridge Stamp
- Creating a Flanged Hole Stamp
- Creating a Circular Stamp
- Creating a Stiffening Rib Stamp
- Creating a Dowel Stamp
- Introduction to DMU Kinematics
- Designing a Mechanism
- Creating the Revolute Joint
- Creating the Prismatic Joint
- Creating the Cylindrical Joint
- Creating the Screw Joint
- Creating the Rigid Joint
- Creating the Spherical Joint
- Creating the Planar Joint
- Creating the Point Curve Joint
- Creating the Slide Curve Joint
- Creating the Roll Curve Joint
- Creating the Point Surface Joint
- Creating the Universal Joint
- Creating the CV Joint
- Creating the Gear Joint
- Creating the Rack Joint
- Creating the Cable Joint
- Converting Assembly Constraints into Joints